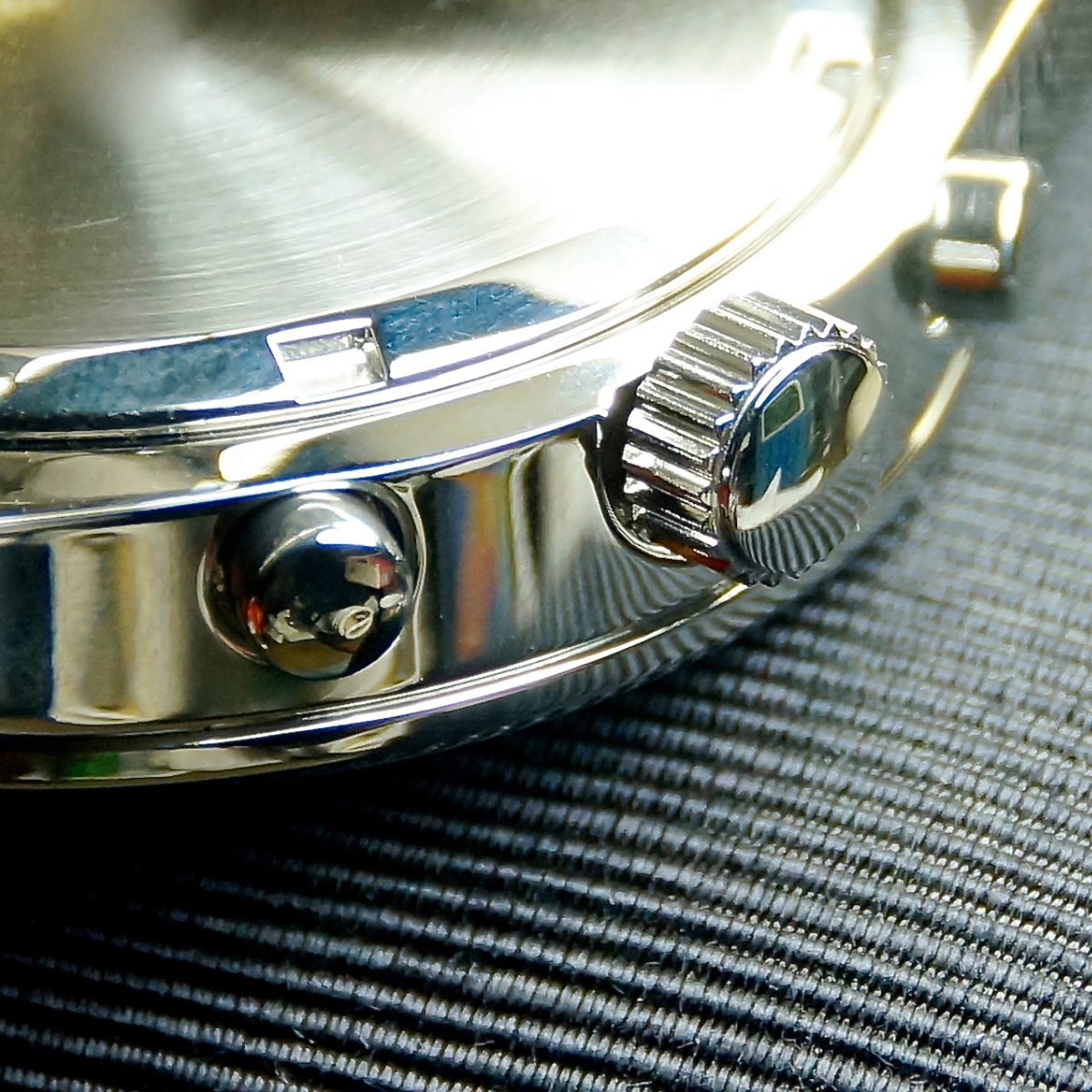
In the video “Making Lathe Mounted Buffing Wheels and Polishing Mops” by Sean Beardon, you will learn how to create lathe wheel mounts in order to utilize homemade knife sharpening wheels. Rather than making just two mounts, Beardon demonstrates how to make six mounts to accommodate felt wheels and various cotton mops for a wide range of uses. The video takes you through the entire process, from cutting bolts to shaping tubes, welding bolts, cutting and drilling plate steel, lathe work, spray time, and finally mopping up. By following along, you will gain the knowledge and skills necessary to create your own lathe mounted buffing wheels and polishing mops.
Click Here To Read About Seiko Watches and Rolex Watches!
Cutting bolts
When it comes to cutting bolts, precision and accuracy are of utmost importance. A poorly cut bolt can compromise the integrity of a structure or machinery, leading to potential safety hazards. To ensure a clean and precise cut, it is essential to use the right tools and techniques.
Tools for cutting bolts
To efficiently cut bolts, you need to have proper tools at your disposal. One of the most commonly used tools for this purpose is a bolt cutter. Bolt cutters come in various sizes and designs, but the basic principle remains the same – a pair of lever-type jaws that can cut through bolts with ease. Additionally, you might also need a hacksaw or a reciprocating saw, depending on the size and thickness of the bolts you are working with.
Techniques for cutting bolts
Before cutting a bolt, it is crucial to measure and mark the desired length accurately. Using a ruler or a tape measure, mark the point where you want to cut the bolt. For smaller bolts, a bolt cutter can be used by placing the jaws around the bolt at the marked point and applying downward pressure. If the bolt is larger or thicker, a hacksaw or reciprocating saw might be more suitable. Remember to use appropriate safety equipment, such as goggles and gloves, to protect yourself during the cutting process.
Shaping tube
Shaping tubes is a common task in various industries, including construction, automotive, and manufacturing. Whether you need to create precise angles or curves, having the right techniques and tools can make a significant difference in the final outcome.
Tools for shaping tube
To shape tubes effectively, you might need a variety of tools. One essential tool is a tube bender, which allows you to create smooth bends without causing damage or deformation to the tube. Tube benders come in various sizes and styles, including manual and hydraulic options. Additionally, a tube notcher is necessary for creating precise cuts and notches in the tube, enabling accurate fitting and joining of multiple tubes.
Techniques for shaping tube
Before shaping a tube, it is crucial to measure and mark the desired angles and curves accurately. Using a protractor or angle finder, determine the exact angles needed for the specific application. Depending on the complexity of the shape, you can use a tube bender to create the desired bends. Start by placing the tube into the bender and adjusting the settings to achieve the desired angle. Slowly apply pressure to the bender and ensure the tube is evenly shaped. For notching, a tube notcher can be used to cut out precise sections from the tube, allowing for seamless fitting and joining with other tubes.
Welding bolt
Welding bolts is a common practice when it comes to joining metal components securely. Whether you are working on a construction project, automotive repair, or manufacturing application, having the right knowledge and skills for welding bolts is essential for maintaining structural integrity.
Tools for welding bolt
To effectively weld bolts, you need to have the appropriate tools and equipment. One of the primary tools needed is a welding machine, which generates the heat necessary for melting and fusing metal components together. Depending on the type of welding, you might need a TIG (Tungsten Inert Gas) welder, MIG (Metal Inert Gas) welder, or stick welder. Additionally, a wire brush or grinder is essential for preparing the surface of the bolt for welding by removing any rust, dirt, or paint.
Techniques for welding bolt
Before welding a bolt, it is crucial to properly prepare the surfaces to be joined. Begin by cleaning the bolt thoroughly using a wire brush or grinder to remove any contaminants. Once the surfaces are clean, position the bolt in the desired location and secure it using clamps or a vise. Adjust the welding machine settings according to the type and thickness of the metal bolts are made of. Start the welding process by creating an arc between the welding electrode and the bolt, ensuring a smooth and consistent bead. Monitor the weld pool closely to achieve uniform penetration and fusion between the bolt and the metal surface.
Click Here To See More Luxury Watches.
Cutting and drilling plate steel
Working with plate steel is a common task in industries such as construction, manufacturing, and fabrication. Whether you need to create precise cuts or holes for specific applications, having the right tools and techniques is crucial for a successful outcome.
Tools for cutting and drilling plate steel
To cut and drill plate steel effectively, you need to have certain tools at your disposal. One of the primary tools needed is a plasma cutter, which utilizes a concentrated jet of hot plasma to cut through metal. Plasma cutters offer excellent precision and speed, making them suitable for various thicknesses of plate steel. Additionally, a high-quality drill press with various drill bits is essential for drilling accurate holes in the steel.
Techniques for cutting and drilling plate steel
Before cutting plate steel, it is essential to measure and mark the desired cuts accurately. Using a ruler or a tape measure, mark the lines where the cuts are to be made. Familiarize yourself with the specific settings and operation of the plasma cutter to ensure safety and precise cutting. Position the plasma cutter torch at the starting point of the marked line and initiate the cutting process. Move the torch at a steady pace along the marked line, allowing the plasma cutter to make a clean, accurate cut. For drilling holes in plate steel, secure the steel piece firmly on the drill press table and select the appropriate drill bit for the desired hole size. Align the drill bit with the marked spot and gradually feed it into the steel using the drill press.
Lathe work
Lathe work is a fundamental aspect of machining and is utilized to create cylindrical shapes with precise dimensions. Whether you are working with metal, wood, or other materials, having the right techniques and tools for lathe work is essential for achieving accurate results.
Tools for lathe work
To perform lathe work effectively, you need essential tools and equipment. The primary tool required is a lathe machine, which rotates the workpiece and allows you to shape it with cutting tools. Lathe machines come in various sizes, ranging from small tabletop models to large industrial machines. Additionally, a set of high-quality lathe cutting tools, including different types of turning, facing, and threading tools, is necessary for achieving various machining tasks.
Techniques for lathe work
Before starting lathe work, it is crucial to securely mount the workpiece to the lathe machine’s chuck or faceplate. Ensure that the workpiece is centered and aligned properly to avoid vibration or wobbling during the machining process. Select the appropriate cutting tool for the desired machining operation, such as turning, facing, or threading. Set the lathe machine’s speed and feed rate according to the material being machined and the desired level of precision. Slowly engage the cutting tool with the rotating workpiece, using proper tool angles and feed rates. Monitor the machining process closely to achieve the desired dimensions and surface finish.
Spray time
When it comes to achieving a smooth and professional finish on surfaces, spraying is a popular technique widely used in various industries. Whether you are painting a wall, applying a protective coat, or adding a decorative finish, understanding the proper spraying techniques is crucial for obtaining excellent results.
Tools for spraying
To achieve optimal spraying results, you need to have the right tools and equipment at your disposal. The primary tool required is a high-quality spray gun, capable of delivering an even and consistent spray pattern. Spray guns come in different types, such as conventional, HVLP (High Volume Low Pressure), and airless. Additionally, an air compressor or a pressure pot is necessary for providing the required air or fluid pressure to the spray gun.
Techniques for spraying
Before starting the spraying process, it is essential to properly prepare the surface by cleaning, sanding, and applying appropriate primers if necessary. Mix the paint or coating material following the manufacturer’s instructions, ensuring the right consistency and viscosity. Adjust the spray gun settings, such as fluid flow, air pressure, and spray pattern, according to the specific application and desired finish. Hold the spray gun at the recommended distance from the surface and apply the spray in smooth, overlapping strokes, maintaining a consistent speed and distance. To achieve an even finish, move the spray gun systematically, ensuring complete coverage without excessive build-up or runs. Allow sufficient drying or curing time before handling or further processing the sprayed surface.
Mopping up
After completing various tasks and projects, it is crucial to perform proper cleaning and maintenance to ensure a safe and organized work environment. Mopping up involves tidying up the workspace, disposing of waste materials appropriately, and maintaining tools and equipment for future use.
Cleaning the workspace
One of the first steps in mopping up is to clean the workspace thoroughly. Remove any debris, such as wood chips, metal shavings, or excess paint, to minimize hazards and maintain a clean working environment. Sweep or vacuum the floor to eliminate dust and dirt, ensuring a tidy and safe workspace.
Waste disposal
Proper waste disposal is essential for maintaining cleanliness and environmental responsibility. Separate waste materials into appropriate bins for recycling or disposal according to local regulations. Dispose of hazardous materials, such as chemicals or solvents, in designated containers for safe and environmentally-friendly handling.
Tool and equipment maintenance
To prolong the lifespan and performance of your tools and equipment, proper maintenance is crucial. Clean tools and equipment after each use, removing any dirt, debris, or residues that may affect performance or safety. Inspect tools for any signs of damage or wear and perform necessary repairs or replacements. Additionally, lubricate moving parts, such as gears or bearings, to ensure smooth operation and prevent premature failure.
Demo
When showcasing your skills or products, performing a demonstration can be an effective way to convey information and create a memorable experience for your audience. Whether you are demonstrating a new technique, showcasing a cutting-edge tool, or presenting a product’s features and benefits, careful planning and execution are essential for a successful demonstration.
Planning the demo
Before conducting a demo, it is essential to plan and outline the key points and objectives you want to achieve. Define the purpose of the demo and identify the target audience to tailor your presentation accordingly. Determine the appropriate setting, equipment, and materials needed for the demo. Create a script or an outline to guide you through the demonstration, ensuring a clear and structured delivery of information.
Execution of the demo
During the demo, it is crucial to engage your audience and maintain their interest throughout the presentation. Begin by providing an overview of what will be demonstrated and the expected outcomes. Clearly explain the steps and techniques involved, providing detailed explanations and any relevant tips or tricks. Demonstrate the process or use of the tool/product in a controlled and organized manner, ensuring all essential points are covered. Encourage audience participation by answering questions and addressing any concerns or challenges they may have. Finally, conclude the demo by summarizing the key takeaways and offering additional resources or opportunities for further exploration.
My bench grinder
A bench grinder is a versatile tool commonly found in workshops and garages, providing a range of functions and applications. Whether you need to sharpen tools, remove rust, or shape metal, a bench grinder is a valuable addition to your toolkit.
Features and components
A typical bench grinder consists of two grinding wheels mounted on a spindle, driven by an electric motor. The grinding wheels vary in size and composition, with coarse and fine grit options available. Some bench grinders also include additional features such as eye guards, spark deflectors, and adjustable tool rests for enhanced safety and convenience.
Applications
The primary application of a bench grinder is grinding and sharpening various tools, including chisels, drill bits, and knives. The coarse grinding wheel is used for initial shaping and removing material, while the fine grinding wheel provides a smooth and precise finish. In addition to tool sharpening, a bench grinder can also be used for rust removal, deburring, and even light metal shaping tasks.
Safety precautions
When using a bench grinder, it is crucial to prioritize safety to avoid accidents or injuries. Always wear safety goggles or a face shield to protect your eyes from flying sparks and debris. Ensure that the grinding wheels are properly balanced and securely mounted to prevent sudden dislodgment. Use the appropriate tool rests and guards to maintain a safe distance from the grinding wheels during operation. Additionally, avoid excessive pressure on the grinding wheels and maintain a steady hand to prevent accidental slips or entanglement with the rotating wheels.
My camera gear
Having the right camera gear is essential for capturing high-quality images and videos. Whether you are a professional photographer, videographer, or simply an enthusiast, investing in the right equipment can take your visual content to the next level.
DSLR or mirrorless camera
The centerpiece of any camera gear collection is the camera itself. Two popular options are DSLR (Digital Single-Lens Reflex) and mirrorless cameras. DSLR cameras utilize a mirror and prism system, providing optical viewfinders and excellent autofocus performance. On the other hand, mirrorless cameras eliminate the need for mirrors, resulting in smaller and lighter bodies, electronic viewfinders, and advanced video capabilities. Consider your specific needs and preferences to choose the camera type that suits you best.
Lenses
The choice of lenses can significantly impact the quality and versatility of your images and videos. Different lenses offer various focal lengths, aperture capabilities, and overall image quality. A wide-angle lens is ideal for capturing expansive landscapes or architecture, while a telephoto lens enables you to zoom in on distant subjects with clarity. Additionally, a prime lens with a fixed focal length can provide exceptional image quality and low-light performance.
Tripod and accessories
To achieve stability and eliminate camera shake, a tripod is an essential accessory for photographers and videographers. Look for a sturdy and adjustable tripod to support your camera and allow for versatile positioning. Other accessories such as lens filters, external flashes, remote shutter releases, and camera bags can enhance your shooting capabilities, protect your equipment, and provide greater control over your creative vision.
In conclusion, mastering various techniques and utilizing the right tools are crucial elements in the cutting, shaping, welding, and machining processes. Understanding the proper techniques for cutting bolts, shaping tubes, welding bolts, cutting and drilling plate steel, lathe work, and spray painting allows professionals to achieve precise and high-quality results. Additionally, incorporating effective cleaning and maintenance practices, conducting engaging demonstrations, and using appropriate camera gear contribute to a safe and productive work environment. With continuous practice, knowledge, and the right resources, you can elevate your skills and achieve professional outcomes in your selected field.
Is The Rolex Submariner Better – Click Here to Learn More!